The Evolution and Impact of Plastic Injection Molding Manufacturing
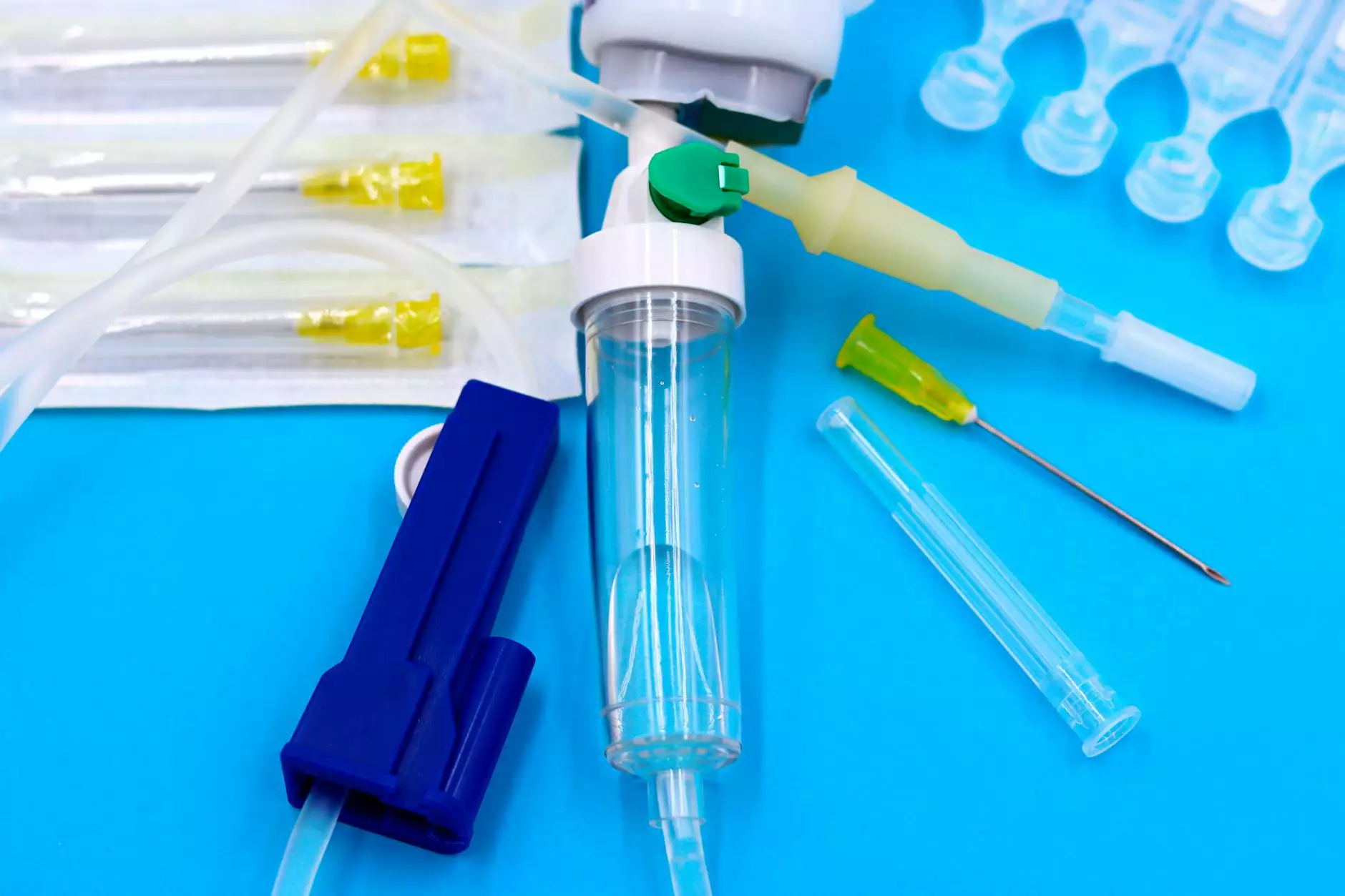
In the manufacturing world, few processes are as pivotal as plastic injection molding manufacturing. This technique has revolutionized the way products are created, allowing for high efficiency, precision, and versatility. In this comprehensive article, we will delve deep into the intricacies of plastic injection molding, exploring its history, process, advantages, applications, and future trends.
Understanding Plastic Injection Molding
Plastic injection molding is a method where molten plastic is injected into a mold to form various products. It is known for its ability to produce large quantities of items with incredibly consistent quality. The process involves several stages, including:
- Material Preparation: Raw plastic pellets are prepared, often blended with colorants or additives to enhance properties.
- Melting: The pellets are heated in a barrel until they reach a molten state.
- Injection: The liquid plastic is injected into a precisely designed mold at high pressure.
- Cooling: Once filled, the mold is cooled, allowing the plastic to solidify in the desired shape.
- Demolding: Finally, the finished product is ejected from the mold.
A Brief History of Plastic Injection Molding
The history of plastic injection molding dates back to the early 20th century. The first patent for an injection molding machine was awarded to John Wesley Hyatt in 1872. However, it wasn't until the 1930s that the process began to take off with the advent of thermoplastics. The introduction of materials such as Polyvinyl Chloride (PVC) and Polyethylene expanded the possibilities for product design and manufacturing.
Why Choose Plastic Injection Molding?
There are several reasons why plastic injection molding is favored by manufacturers across various industries:
- Efficiency: Once a mold is created, the production of each part is rapid, significantly reducing time-to-market.
- Cost-Effectiveness: While the initial cost of molds can be high, the low cost per piece on large runs makes it economically viable.
- Precision and Quality: The process ensures that parts are made to exact specifications with minimal defects.
- Material Variety: A wide array of plastic materials can be used, allowing for customization based on product needs.
- Design Flexibility: Complex shapes and intricate designs can be achieved, opening up creative possibilities for product developers.
Applications of Plastic Injection Molding Manufacturing
The applications of plastic injection molding manufacturing are vast and varied. Here are a few critical sectors that rely heavily on this process:
- Consumer Goods: From toys to home appliances, many everyday items are produced using injection molding.
- Automotive Industry: Components such as dashboards, bumpers, and interior fittings are expertly molded for durability and aesthetic.
- Medical Devices: Precise and sterile components are crucial in healthcare, and injection molding meets these stringent requirements.
- Electronics: Housings for various electronic devices are efficiently manufactured to protect complex circuitry.
- Packaging: From bottles to containers, injection molding produces reliable packaging solutions that keep products safe.
The Future of Plastic Injection Molding Manufacturing
As technology advances, the future of plastic injection molding manufacturing looks promising. Several trends are shaping this industry, including:
- 3D Printing Integration: The combination of injection molding with 3D printing is leading to more rapid prototyping and customized solutions.
- Sustainability Initiatives: There is a growing emphasis on using recycled materials and reducing waste in the injection molding process.
- Automation and Smart Manufacturing: Automation in injection molding processes enhances efficiency and allows for real-time monitoring of production.
- Rapid Prototyping: Companies are increasingly adopting rapid prototyping methods to bring products to market faster, combining speed with quality.
Challenges Facing Plastic Injection Molding Manufacturing
Despite its many advantages, the plastic injection molding industry faces several challenges:
- High Initial Costs: The expense of creating molds can be prohibitive for smaller businesses, limiting access to this technology.
- Material Limitations: Some applications may require materials that cannot withstand the pressures involved in existing injection molding techniques.
- Environmental Concerns: With increasing scrutiny on plastic usage and waste, manufacturers are challenged to produce more sustainable options.
Conclusion: Embracing the Future of Manufacturing
Plastic injection molding manufacturing has evolved dramatically over the years and remains a cornerstone of modern manufacturing due to its efficiency, versatility, and scalability. As industries advance and adopt new technologies, the future of plastic injection molding looks brighter than ever. By addressing challenges and embracing innovation, manufacturers can harness the potential of this process to meet the ever-growing demands of consumers and industries alike.
For more information on plastic injection molding manufacturing, exploration of Deep Mould provides valuable insights and quality services, ensuring that companies stay ahead in this competitive market.